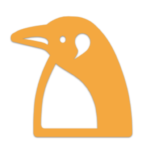
スマートファクトリー化は何から始めたらいいの?
結局なにができるようになるの?
今回はこういった疑問に答えていきます!
昨今、製造業界では「スマートファクトリー」や「DX」に注目が集まっています。
一部の企業では実際に取り組みを何年も前から始め成果を上げています。しかし、多くの企業は何からやっていいのかわからない、取り組み始めたけど思ったように成果が上がらなく進まない。
という悩みを抱えているのではないでしょうか。
それもそのはずです。専門的な知識を有した人材はなかなか社内にはいないでしょうし、具体的な技術情報はほとんど公開されていません。
技術情報は社内にとどめておくという製造業の風潮も一部の企業を除いて、スマートファクトリー化の浸透を妨げています。
筆者は、製造業の技術職に8年間勤務後、IT企業に転職をしています。
クライアント企業へ常駐型でスマートファクトリー化の開発を行っています。
本記事では下記の内容についてまとめています。
- スマートファクトリー化の具体的な取り組み
- スマートファクトリー化を進めていく上での注意点
- スマートファクトリー化を実現した先にあるメリット
スマートファクトリー化の具体的な取り組み
・MES
スマートファクトリー化の実現に向けて注目を集めているのが「MES(Manufacturing Execution System):製造実行システム」です。
MESとは工場の生産、品質、製造、在庫など様々な情報のICT活用の基盤となります。
ICTは情報通信技術の略で、通信技術を活用したコミュニケーションを指します。
今まで製造業では、それぞれの業務に応じてそれぞれのシステムを導入してきました。基幹システムはあるものの、生産管理には生産管理システム、在庫には在庫管理システムと点在しています。
この様々なレガシーシステムの中心に位置をしてシステム間のコミュニケーションを図るのがMESの役割になります。
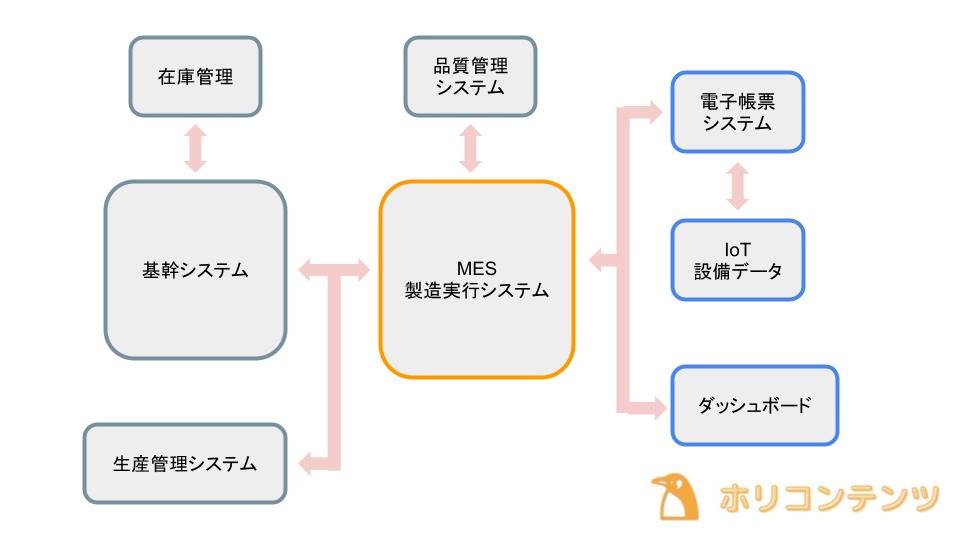
・電子帳票化
現場には始業点検や運転記録表、設備停止情報から品質記録表まで様々な帳票があります。
これらをペーパーレスにします。スマートフォンやタブレットなどのデバイスを用いて記録を行い、データベースに保存できるため、運転記録がそのままデータとして蓄積されていきます。
リアルタイム連携
MESやIoT、BI ツールと連携
生産指示や現場の情報をリアルタイムに共有可能
生産条件や設備データをIoTで瞬時に取得可能
ポカヨケ
入力制限や閾値、判定機能を利用することで人為的なミスを軽減可能
生産条件を閾値で管理できるため、誤品を防止
帳票の転記工数の削減
作業実績や条件、設備停止情報などはデータベースに保存
BIツールと連携してKPIなどをグラフ化まで自動化が可能
・設備、センサー類のIoT化
工場にある様々な設備と接続し、データの収集や加工、データベースへの保存を行います。
遠隔で設備情報を取得
データを可視化して離れた場所からでも異常検知が可能
パトライト等の連携も容易に可能
各種データの蓄積
時系列で設備データを蓄積することで季節要因などを踏まえた分析が可能
故障予知やAIの活用に必須
システム間の連携
電子帳票と連携することで設備データを瞬時に取得可能
設備点検値や実績値の取得工数を大幅に削減
・見える化
BIツールを活用して企業が持っているデータを使いビジネス上の洞察を得ます。
ダッシュボードにデータを見える化することで、意思決定を的確にかつ迅速に行うことができます。
工場が持つデータにはExcelからCSV、各種システムのデータベースなど様々です。BIツールを用いれば全てのデータに接続して見える化が可能です。
[関連記事]
【Tableau×製造業】製造業でのTableau活用事例あり!導入するメリットは?BIツールとは?
【製造業】失敗しない!BIツールの導入においておさえておきたい7つの選定ポイント
・機械学習、AIの活用
蓄積したデータを用いて作成したモデルから予知保全や予測を行うことができます。
作成したモデルを使って設備の稼働データを常時分析することで設備が不具合を起こすタイミングを予測します。
設備の不具合で製造ラインを止めてしまうことなどを防げるため、不具合に対して先手で対処できるAI・機械学習の活用に注目が集まっています。
進め方の順番と注意点
費用対効果がすぐには出てこないスマートファクトリー化において、プロジェクトの頓挫を避けるためにもスモールスタートが重要です。
せっかく取り組み始めたのに費用・工数の不足により効果出しがうまくできずに頓挫してしまうことを避けるためにも段階を踏んで取り組むことが重要です。
「スマートファクトリー化の具体的な取り組み」を推奨する順番に並べてご紹介します。
現場のリアルな情報をデータベースに蓄積するフローの構築
現在あるデータを使い見える化を実施
PLCなど様々なFA機器のデータを電子帳票連携や見える化
時系列データをデータベースに蓄積するフローの構築
システム間の連携を可能にするICT活用の基盤づくり
基幹システムと電子帳票の連携など
蓄積されたデータから統計的手法、人工知能を活用して予測分析を実施
設備の予知保全など
実現した先にあるメリット
・帳票作成の工数削減
事務所と現場での紙帳票の受け渡しが無くなります。
ICT活用の基盤ができると管理側が発行する生産指示書や現場で作成する始業点検や生産記録のやりとりが全てデータで行えるようになります。
帳票の受け渡しや保管、転記する工数が削減できます。
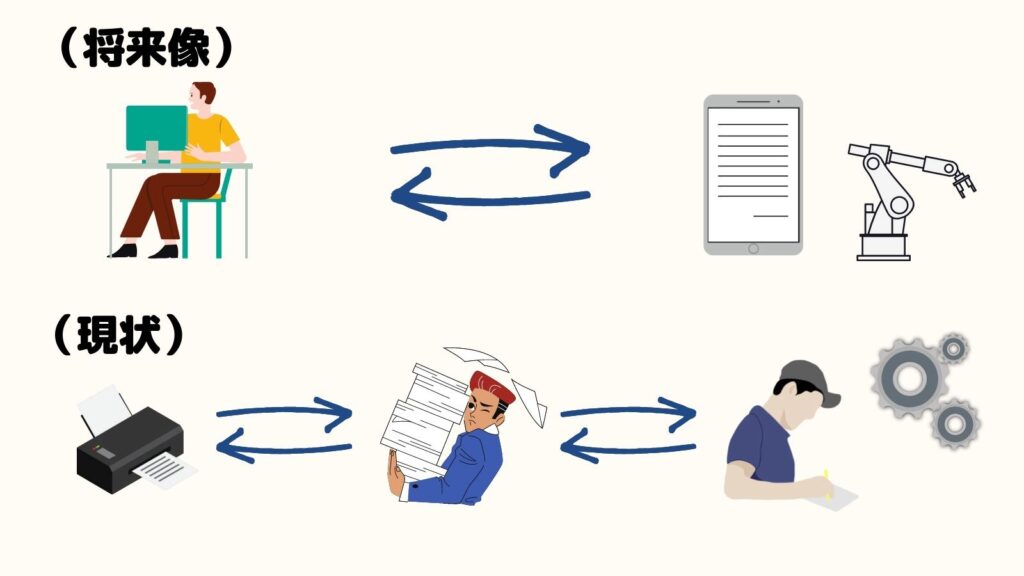
・現場の異常をリアルタイムに把握
生産状況や設備停止情報、在庫情報など様々な情報をリアルタイムに把握できるため、管理者は先手に対策を打つことが出来ます。
生産計画に対して遅れはないか、遅れている場合何が原因で遅れているのかなど従来は現場に出向き作業者に聞き取りを行う必要がありました。
データの可視化により事務所にいながら自分のPCでそれらの情報を得ることが可能になります。
・不良率の低減
生産条件や計測値などをデータ取込みとすることで、異常を見逃さない仕組みができます。
生産条件の閾値管理や、電子帳票等では次に進めない仕組みとすることで、確実に上司へ報告がいくようにして、不良品の作成を防止します。
また、抜き取り検査などの品質データも即時に現場作業者へ送付することができるため、素早く対策を打つことができるようになります。
・工程の稼働率向上
設備やセンサーの値の見える化でどこからでも異常に気付けるため、早期に対策が打てます。
現場の大型モニターに映し出して閾値を超えたらパトランプを回すなどの仕組みが簡単にできようになります。
近年のIoTツールは工場にある様々なFA機器と繋がることができます。
また、蓄積した設備やセンサーのデータでAI・機械学習を用いることで、故障や部品交換時期を予測することができるため、事前に部品を調達して設備停止を未然に防ぐことができます。
課題
電子帳票化やIoT、見える化を実施していく上で少なからずプログラミングやデータベースの知識が必要になります。
そのため、製造業にとってはIT人材の確保が課題になるでしょう。
主に、pythonやSQLといった専門的な知識やサーバーでの作業が必要になります。
開発をベンダーに頼むケースが多いかと思いますが、現場の運用を全く知らないエンジニアとでは意思疎通がうまく出来なかったり、修正や保守のたびに費用がかかってしまうため得策ではありません。
そのため、可能な限り自社の人材で開発を行える環境を作ることがとても大事になります。
近年、ノンプログラミングで開発ができるツールが出てきていますので、そういった選定もスマートファクトリーを推進する上で非常に重要になります。
まとめ
今回はスマートファクトリー化に基づく様々な施策をご紹介しました。
失敗しないためにも、自社工場の現状把握からしっかり行っていきましょう。
データに基づく意思決定や予測分析を行おうと思っても、デジタル形式で保存されている生データがなければ実現は不可能です。
何から初めればいいのかという検討にこの記事が役に立てましたら大変うれしく思います。